Linde Unveils its Partnership with Ariane Group to Vivify the AM Process for Copper Alloys
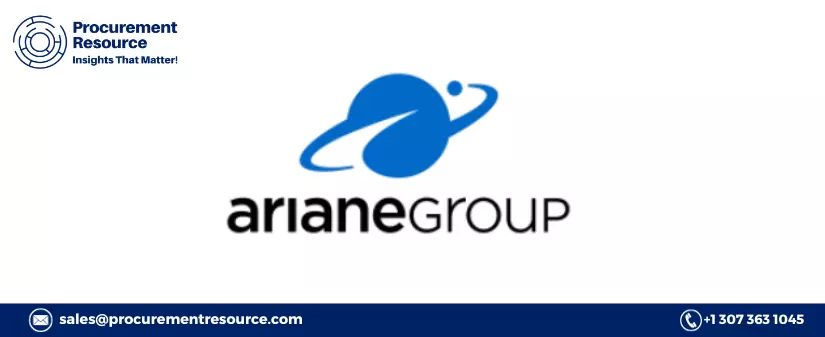
Linde, a global industrial gas and engineering company, has recently announced a strategic collaboration with Ariane Group, a leading civil and defence space launcher system contractor. The primary focus of this collaboration is to advance the additive manufacturing (AM) process for copper alloys, with an ultimate aim to utilize them in the engine combustion chambers of future heavy-lift rockets.
Additive manufacturing has revolutionized the aerospace industry, now allowing for the fabrication of complex copper engine components, such as cooling channels, which were formerly deemed unattainable. Copper, renowned for its superior heat conductivity vital for aerospace applications, presents unique challenges in 3D printing. The metal's inherent properties cause it to reflect lasers, thus demanding high-intensity laser beams that risk overheating and subsequent oxidation.
Addressing this challenge, Linde is bringing its proprietary gas mixture, ADDvance Laser230, and its advanced oxygen control system, ADDvance O2 precision, to the table. The collaboration with Ariane will see the testing of an enhanced AM process aimed at achieving high-precision and top-quality printed copper components.
Speaking on the new venture, Pierre Foret, Associate Director of AM at Linde, expressed immense pride in the collaboration. He remarked, "Cooperating with globally renowned partners like Ariane stands central to Linde’s ethos of innovation." ADDvance Laser230 is designed to augment the laser powder bed fusion (LPBF) printing. Its unique argon-helium blend optimizes the process by minimizing fumes and spatters, thus accelerating cycles, enhancing reliability, and cutting down costs. Linde asserts that this blend's versatility makes it compatible with any alloy, especially for intricate AM structures.
Furthermore, the ADDvance O2 precision system maintains a low residual oxygen level, which helps prevent overheating and oxidation. This, in turn, facilitates a more streamlined printing process without mandatory cooling periods between layers. An added advantage is the ability to reuse non-oxidised powder, leading to substantial savings in material costs.
Mathis Palm, a Process Specialist at Ariane Group, emphasized the significance of improved AM processes for ensuring the cost-effectiveness and efficiency of future rocket engines. He expressed confidence in Linde’s gas expertise playing a pivotal role in refining the AM process.
Ariane Group, with a commendable history of launching satellites into orbit, has showcased its proficiency in space exploration, particularly with the Ariane 5 and Vega C Rockets. The group, backed by the European Space Agency (ESA), has consistently demonstrated its commitment to pushing boundaries in aerospace innovation.
According to the article by Procurement Resource, Linde and Ariane Group have embarked on a collaboration to advance the additive manufacturing (AM) process for copper alloys in rocket engine combustion chambers. Given copper's laser-reflective properties, AM of such alloys was a challenge.
Linde introduces its proprietary gas mixture, ADDvance Laser230, and the ADDvance O2 precision system to refine the process. These innovations optimize the laser powder bed fusion printing, reduce oxidation, speed up cycles, and allow the reuse of non-oxidised powder, decreasing costs. Pierre Foret of Linde underscored the importance of such partnerships for innovation, while Mathis Palm from Ariane Group acknowledged the role of Linde's gas expertise in enhancing AM processes.