Cotton Production Cost Reports
Agriculture, Farming and Commodity
The report provides a detailed analysis essential for establishing a cotton manufacturing plant. It encompasses all critical aspects necessary for cotton production, including the cost of cotton production, cotton plant cost, cotton production costs, and the overall cotton manufacturing plant cost. Additionally, the study covers specific expenditures associated with setting up and operating a cotton production plant. These encompass manufacturing processes, raw material requirements, utility requirements, infrastructure needs, machinery and technology requirements, manpower requirements, packaging requirements, transportation requirements, and more.
Cotton is a natural plant-based fabric material mainly associated with the textile and clothing sector. The fabric is soft, comfortable, and is skin-friendly. It is considered to produce a variety of clothing materials. Cotton is used to produce jackets, Custom t-shirts, shirts, socks, handkerchiefs, trousers, and more.
The fabric is used to manufacture homewares such as bedsheets, curtains, tablecloths, and more. It is also utilized in producing industrial products such as tents, tarpaulins, etc. Additionally, the material is an ideal fabric to be used as a long-lasting fabric, ensuring comfort. Hence, it is utilized in making defense uniforms and space clothing.
The market for cotton is majorly driven by its demand as a skin-friendly fabric material in the textile and fabric industries. Its usage in the production and designing of clothing varieties, starting from vests to trousers, propel its demand in the market. It is a versatile, organic, and comfortable fabric variety that can be combined with other fabric varieties to produce hybrid fabrics.
Its usage in the production of cotton-polyester fabric, cotton-linen blend, cotton-rayon variety, etc., boosts its demand in the textile and fabric sectors. Industrial cotton procurement is dependent upon various factors, including its demand as a fabric material, along with its production (that is dependent upon the weather conditions), logistics, and more.
Another prominent factor, such as its market prices and supply, also impacts its procurement on a large scale. Hence, changes in these factors, specifically in its demand as a fabric material in the textile industry, as well as the variation in its market prices and distribution, have a significant impact on its procurement.
Raw Material for Cotton Production
According to the cotton manufacturing plant project report, the key raw material for cotton production includes cotton seeds.
Manufacturing Process of Cotton
The extensive cotton production cost report consists of the major industrial manufacturing process:
- By Agricultural Method: The production process of cotton is initiated by cultivating cotton seeds. The brown to black colored seeds obtained from cotton plants are sown at a particular period, and then harvested during kharif season.
Cotton is one of the most commonly known fabrics that are widely considered to manufacture comfortable and airy clothing on a wide range. The fiber is obtained from the cotton plants that are grown from the seeds of cotton. The plant requires a warm climatic condition and is generally planted during the springs. The plants require lots of heat and a humid atmosphere. Sandy, loamy soil with an adequate clay content, provides the plant with required nourishments and allows good growth. Cotton can be harvested five to six months after the plantation.
The cotton obtained from the plant then undergoes complex sequential processes that finally yield cotton fabric, which is widely used in the textile industries. Initially, the fiber is mechanically cleaned by passing through several rollers and screens that separate the cotton seeds while maintaining the moisture of the fiber.
The process is termed an enhanced volume output cleaner, or EVOC, which is designed to clean the impurities in the fiber. Then, the resultant is treated with a chemical solution that loosens and cleans the fiber from dust, oil, and other particles. It is then rinsed with water to remove the chemical traces. It is then processed through purification and finishing, where the fiber is treated with detergent and then undergoes spinning, heat treatment, stretching, and drying. The final product is then marketed in the global market.
Cotton Production Cost Processes with Cost Analysis
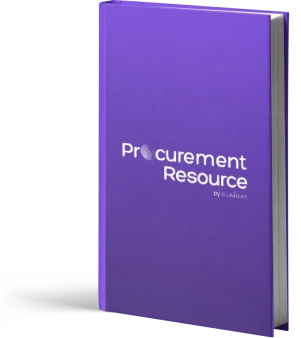
Cotton Production by Agricultural Methods
This study analyzes Cotton Production by Agricultural Methods, covering manufacturing, process flow, operating expenses, and financial considerations.
Details: Germany - based plant Q1 2025 From $ 2499.00 USD
Product Details
Particulars | Details |
---|---|
Product Name | Cotton |
Scope | Manufacturing Process: Process Flow, Material Flow, Material Balance Raw Material and Product Specifications: Raw Material Consumption, Product and Co-product Generation Land and Site Cost: Offsites/Civil Works, Equipment Cost, Auxiliary Equipment Costs, Contingency, Engineering and Consulting Charges, Working Capital Variable Cost: Raw Material, Utilities, Other Variable Costs Fixed Cost: Labor Requirements and Wages, Overhead Expenses, Maintenance Charges, Other Fixed Costs Financing Costs: Interest on Working Capital, Interest on Loans Other Costs: Depreciation Charges, General Sales and Admin Cost |
Currency | US$ (Data can also be provided in the local currency) |
Pricing and Purchase Options | Basic: US$ 2499 Premium: US$ 3499 Enterprise: US$ 4799 |
Customization Scope | The report can be customized as per the requirement of the customer |
Post-Sale Analysts Report | 10-12 weeks of post-purchase analyst support after report delivery for any queries from the deliverable |
Delivery Format | PDF and Excel format through email (editable version in PPT/Word format of the report can be also provided on special request) |
How does our Cotton Production Cost Report Provide Exhaustive Data and Extensive Insights?
At Procurement Resource, we not only focus on optimizing the should cost of production for Cotton but also provide our clients with extensive intel and rigorous information on every aspect of the production process. By utilizing a comprehensive cost model, we help you break down expenses related to raw materials, labor, and technology, offering clear pathways to savings. We also assist in evaluating the capital expenditure (CAPEX) and operating expenses (OPEX), which are often measured as cost per unit of production, such as USD/MT, ensuring that your financial planning is aligned with industry benchmarks.
We offer valuable insights on the top technology providers, in-depth supplier database, and best manufacturers, helping you make informed decisions to improve efficiency. Additionally, we design the most feasible layout for your production needs, ensuring the entire process runs smoothly. By minimizing the cash cost of production, we ensure that you stay competitive while securing long-term profitability in the growing Cotton market. Partnering with Procurement Resource guarantees that every aspect of your production is cost-efficient, advanced, and tailored to your specific requirements.
Key Questions Answered in This Report
- What are the key requirements for setting up a Cotton manufacturing plant?
- How is Cotton manufactured?
- What is the process flow involved in producing Cotton?
- What are the raw material requirements and costs for producing Cotton?
- What is the total size of land required for setting up a Cotton manufacturing plant?
- What are the construction requirements for setting up a Cotton manufacturing plant?
- What are the machinery requirements for producing Cotton?
- What are the utility requirements and costs for producing Cotton?
- What are the manpower requirements for producing Cotton?
- What are the average salaries/wages of manpower working in a Cotton manufacturing plant?
- What are the packaging requirements and associated costs for Cotton?
- What are the transportation requirements and associated costs for Cotton?
- What are the capital costs for setting up a Cotton manufacturing plant?
- What are the operating costs for setting up a Cotton manufacturing plant?
- What should be the price of Cotton?
- What will be the income and expenditures for a Cotton manufacturing plant?
Need more help?
- We can tailor the report as per your unique requirements such as desired capacity, future expansion plans, product specifications, mode of financing, plant location, etc.
- We can also provide a flexible, easy-to-use, dynamic excel-based cost-model/ dashboard where you can change the inputs to get different outputs
- Speak to our highly skilled team of analysts for insights on the recent trends and innovations, industry best practices, key success and risk factors, product pricing, margins, return on investment, industry standards and regulations, etc.
- Gain an unparalleled competitive advantage in your domain by understanding how to optimize your business operations and maximize profits
- For further assistance, please connect with our analysts
Compare & Choose the Right Report Version for You

You can easily get a quote for any Procurement Resource report. Just click here and raise a request. We will get back to you within 24 hours. Alternatively, you can also drop us an email at sales@procurementresource.com.
RIGHT PEOPLE
At Procurement Resource our analysts are selected after they are assessed thoroughly on having required qualities so that they can work effectively and productively and are able to execute projects based on the expectations shared by our clients. Our team is hence, technically exceptional, strategic, pragmatic, well experienced and competent.
RIGHT METHODOLOGY
We understand the cruciality of high-quality assessments that are important for our clients to take timely decisions and plan strategically. We have been continuously upgrading our tools and resources over the past years to become useful partners for our clientele. Our research methods are supported by most recent technology, our trusted and verified databases that are modified as per the needs help us serve our clients effectively every time and puts them ahead of their competitors.
RIGHT PRICE
Our team provides a detailed, high quality and deeply researched evaluations in competitive prices, that are unmatchable, and demonstrates our understanding of our client’s resource composition. These reports support our clientele make important procurement and supply chains choices that further helps them to place themselves ahead of their counterparts. We also offer attractive discounts or rebates on our forth coming reports.
RIGHT SUPPORT
Our vision is to enable our clients with superior quality market assessment and actionable evaluations to assist them with taking timely and right decisions. We are always ready to deliver our clients with maximum results by delivering them with customised suggestions to meet their exact needs within the specified timeline and help them understand the market dynamics in a better way.
SELECT YOUR LICENCE TYPE
- Review the available license options and choose the one that best fits your needs. Different licenses offer varying levels of access and usage rights, so make sure to pick the one that aligns with your requirements.
- If you're unsure which license is right for you, feel free to contact us for assistance.
CLICK 'BUY NOW'
- Once you've selected your desired report and license, click the ‘Buy Now’ button. This will add the report to your cart. You will be directed to the registration page where you’ll provide the necessary information to complete the purchase.
- You’ll have the chance to review your order and make adjustments, including updating your license or quantity, before proceeding to the next step.
COMPLETE REGISTRATION
- Enter your details for registration. This will include your name, email address, and any other necessary information. Creating an account allows you to easily manage your orders and gain access to future purchases or reports.
- If you already have an account with us, simply log in to streamline the process.
CHOOSE YOUR PAYMENT METHOD
- Select from a variety of secure payment options, including credit/debit cards, PayPal, or other available gateways. We ensure that all transactions are encrypted and processed securely.
- After selecting your payment method, you will be redirected to a secure checkout page to complete your transaction.
CONFIRM YOUR PURCHASE
- Once your payment is processed, you will receive an order confirmation email from sales@procurementresource.com confirming the dedicated project manger and delivery timelines.
ACCESS YOUR REPORT
- The report will be delivered to you by the project manager within the specified timeline.
- If you encounter any issues accessing your report, project manager would remain connected throughout the length of the project. The team shall assist you with post purchase analyst support for any queries or concerns from the deliverable (within the remit of the agreed scope of work).