Grey Cast Iron Production Cost Reports
Chemicals
The report provides a detailed analysis essential for establishing a grey cast iron manufacturing plant. It encompasses all critical aspects necessary for grey cast iron production, including the cost of grey cast iron production, grey cast iron plant cost, grey cast iron production costs, and the overall grey cast iron manufacturing plant cost. Additionally, the study covers specific expenditures associated with setting up and operating a grey cast iron production plant. These encompass manufacturing processes, raw material requirements, utility requirements, infrastructure needs, machinery and technology requirements, manpower requirements, packaging requirements, transportation requirements, and more.
Grey Cast Iron is one of the most preferred iron varieties that is used in the commercial sectors. It is a widely used metal material that is incorporated in manufacturing pumps, machinery bases, weights and counterweights, wind turbine housings, other truck parts, truck suspension components, valves, tractor parts, steering knuckles, stove parts, linkages, plough shares, automotive suspension components, hydraulic components, and gears on a large scale.
It is also used to manufacture metal products such as pipe fittings, manhole covers and drainage systems. The metal material is also used in brake rotors, exhaust manifolds and more. The market for grey cast iron is strongly impacted by the variation in its demand as a metal variety that is further used to produce various products that are installed in machineries, used for construction and industrial operations.
Grey cast iron’s usage in the production of metal tools, equipment, including gears, plough shares, stove parts, etc., fuels its demand in the market. Moreover, its moldability and durability, increases its applications across various sectors, and strengthens its market growth. The increasing demand of grey cast iron metal largely influences its procurement.
Industrial grey cast iron procurement is also influenced by various other factors including its production cost, market prices, governmental regulations, trade and transportation activities etc. Therefore, changes in these aspects, specifically in its demand across metal, construction, automobile, electronic and electrical industries, as well as its prices and distributions directly impact its procurement on a large-scale.
Raw Material for Grey Cast Iron Production
According to the grey cast iron manufacturing plant project report, the key raw material for grey cast iron production includes pig iron and cast-iron scrap.
Manufacturing Process of Grey Cast Iron
The extensive grey cast iron production cost report consists of the major industrial manufacturing process:
- From Cast-Iron Scrap and Pig Iron: The production process of grey cast iron is carried out by processing cast-iron scrap and pig iron through melting, molding, cooling, cleaning, and finishing for commercial use.
Grey Cast Iron is an iron metal type which is well known for its grey surface colour that is mainly obtained due to the graphite fractures in the metal material. The graphite flake structure on the metal material is created while processing it through the cooling process due to the carbon present in the component. The properties of grey cast iron change with the variation of materials used to combine and the process that is used for casting the metal.
It is one of the cheapest cast iron metal types, exhibiting good ductility, tensile strength, impact resistance, and yield strength. It has an excellent dampen vibration ability that makes it an ideal metal to be used in machinery bases on a large scale. It exhibits great thermal conductivity and can withstand thermal cycling very well. It possesses low shock resistivity than other casted metal varieties. Its melting point is measured at around 1260° C.
Grey Cast Iron Production Cost Processes with Cost Analysis
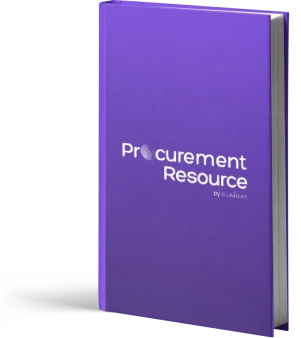
Grey Cast Iron Production from Pig Iron and Cast-Iron Scrap
The study offers a detailed cost analysis of Grey Cast Iron Production from Pig Iron and Cast-Iron Scrap. In addition, the report incorporates the manufacturing process with detailed process and material flow, operating costs along with financial expenses and depreciation charges.
Details: Germany - based plant Q1 2025 From $ 2499.00 USD
Product Details
Particulars | Details |
---|---|
Product Name | Grey Cast Iron |
Scope | Manufacturing Process: Process Flow, Material Flow, Material Balance Raw Material and Product Specifications: Raw Material Consumption, Product and Co-product Generation Land and Site Cost: Offsites/Civil Works, Equipment Cost, Auxiliary Equipment Costs, Contingency, Engineering and Consulting Charges, Working Capital Variable Cost: Raw Material, Utilities, Other Variable Costs Fixed Cost: Labor Requirements and Wages, Overhead Expenses, Maintenance Charges, Other Fixed Costs Financing Costs: Interest on Working Capital, Interest on Loans Other Costs: Depreciation Charges, General Sales and Admin Cost |
Currency | US$ (Data can also be provided in the local currency) |
Pricing and Purchase Options | Basic: US$ 2499 Premium: US$ 3499 Enterprise: US$ 4799 |
Customization Scope | The report can be customized as per the requirement of the customer |
Post-Sale Analysts Report | 10-12 weeks of post-purchase analyst support after report delivery for any queries from the deliverable |
Delivery Format | PDF and Excel format through email (editable version in PPT/Word format of the report can be also provided on special request) |
How does our Grey Cast Iron Production Cost Report Provide Exhaustive Data and Extensive Insights?
At Procurement Resource, we not only focus on optimizing the should cost of production for Grey Cast Iron but also provide our clients with extensive intel and rigorous information on every aspect of the production process. By utilizing a comprehensive cost model, we help you break down expenses related to raw materials, labor, and technology, offering clear pathways to savings. We also assist in evaluating the capital expenditure (CAPEX) and operating expenses (OPEX), which are often measured as cost per unit of production, such as USD/MT, ensuring that your financial planning is aligned with industry benchmarks.
We offer valuable insights on the top technology providers, in-depth supplier database, and best manufacturers, helping you make informed decisions to improve efficiency. Additionally, we design the most feasible layout for your production needs, ensuring the entire process runs smoothly. By minimizing the cash cost of production, we ensure that you stay competitive while securing long-term profitability in the growing Grey Cast Iron market. Partnering with Procurement Resource guarantees that every aspect of your production is cost-efficient, advanced, and tailored to your specific requirements.
Key Questions Answered in This Report
- What are the key requirements for setting up a Grey Cast Iron manufacturing plant?
- How is Grey Cast Iron manufactured?
- What is the process flow involved in producing Grey Cast Iron?
- What are the raw material requirements and costs for producing Grey Cast Iron?
- What is the total size of land required for setting up a Grey Cast Iron manufacturing plant?
- What are the construction requirements for setting up a Grey Cast Iron manufacturing plant?
- What are the machinery requirements for producing Grey Cast Iron?
- What are the utility requirements and costs for producing Grey Cast Iron?
- What are the manpower requirements for producing Grey Cast Iron?
- What are the average salaries/wages of manpower working in a Grey Cast Iron manufacturing plant?
- What are the packaging requirements and associated costs for Grey Cast Iron?
- What are the transportation requirements and associated costs for Grey Cast Iron?
- What are the capital costs for setting up a Grey Cast Iron manufacturing plant?
- What are the operating costs for setting up a Grey Cast Iron manufacturing plant?
- What should be the price of Grey Cast Iron?
- What will be the income and expenditures for a Grey Cast Iron manufacturing plant?
Need more help?
- We can tailor the report as per your unique requirements such as desired capacity, future expansion plans, product specifications, mode of financing, plant location, etc.
- We can also provide a flexible, easy-to-use, dynamic excel-based cost-model/ dashboard where you can change the inputs to get different outputs
- Speak to our highly skilled team of analysts for insights on the recent trends and innovations, industry best practices, key success and risk factors, product pricing, margins, return on investment, industry standards and regulations, etc.
- Gain an unparalleled competitive advantage in your domain by understanding how to optimize your business operations and maximize profits
- For further assistance, please connect with our analysts
Compare & Choose the Right Report Version for You

You can easily get a quote for any Procurement Resource report. Just click here and raise a request. We will get back to you within 24 hours. Alternatively, you can also drop us an email at sales@procurementresource.com.
RIGHT PEOPLE
At Procurement Resource our analysts are selected after they are assessed thoroughly on having required qualities so that they can work effectively and productively and are able to execute projects based on the expectations shared by our clients. Our team is hence, technically exceptional, strategic, pragmatic, well experienced and competent.
RIGHT METHODOLOGY
We understand the cruciality of high-quality assessments that are important for our clients to take timely decisions and plan strategically. We have been continuously upgrading our tools and resources over the past years to become useful partners for our clientele. Our research methods are supported by most recent technology, our trusted and verified databases that are modified as per the needs help us serve our clients effectively every time and puts them ahead of their competitors.
RIGHT PRICE
Our team provides a detailed, high quality and deeply researched evaluations in competitive prices, that are unmatchable, and demonstrates our understanding of our client’s resource composition. These reports support our clientele make important procurement and supply chains choices that further helps them to place themselves ahead of their counterparts. We also offer attractive discounts or rebates on our forth coming reports.
RIGHT SUPPORT
Our vision is to enable our clients with superior quality market assessment and actionable evaluations to assist them with taking timely and right decisions. We are always ready to deliver our clients with maximum results by delivering them with customised suggestions to meet their exact needs within the specified timeline and help them understand the market dynamics in a better way.
SELECT YOUR LICENCE TYPE
- Review the available license options and choose the one that best fits your needs. Different licenses offer varying levels of access and usage rights, so make sure to pick the one that aligns with your requirements.
- If you're unsure which license is right for you, feel free to contact us for assistance.
CLICK 'BUY NOW'
- Once you've selected your desired report and license, click the ‘Buy Now’ button. This will add the report to your cart. You will be directed to the registration page where you’ll provide the necessary information to complete the purchase.
- You’ll have the chance to review your order and make adjustments, including updating your license or quantity, before proceeding to the next step.
COMPLETE REGISTRATION
- Enter your details for registration. This will include your name, email address, and any other necessary information. Creating an account allows you to easily manage your orders and gain access to future purchases or reports.
- If you already have an account with us, simply log in to streamline the process.
CHOOSE YOUR PAYMENT METHOD
- Select from a variety of secure payment options, including credit/debit cards, PayPal, or other available gateways. We ensure that all transactions are encrypted and processed securely.
- After selecting your payment method, you will be redirected to a secure checkout page to complete your transaction.
CONFIRM YOUR PURCHASE
- Once your payment is processed, you will receive an order confirmation email from sales@procurementresource.com confirming the dedicated project manger and delivery timelines.
ACCESS YOUR REPORT
- The report will be delivered to you by the project manager within the specified timeline.
- If you encounter any issues accessing your report, project manager would remain connected throughout the length of the project. The team shall assist you with post purchase analyst support for any queries or concerns from the deliverable (within the remit of the agreed scope of work).