Maltose Production Cost Reports
Food and Beverages
The report provides a detailed analysis essential for establishing a Maltose manufacturing plant. It encompasses all critical aspects necessary for Maltose production, including the cost of Maltose production, Maltose plant cost, Maltose production costs, and the overall Maltose manufacturing plant cost. Additionally, the study covers specific expenditures associated with setting up and operating a Maltose production plant. These encompass manufacturing processes, raw material requirements, utility requirements, infrastructure needs, machinery and technology requirements, manpower requirements, packaging requirements, transportation requirements, and more.
Maltose is a disaccharide used for various food-related applications. In the food industry, it is used as a mild sweetening agent in candies, baked goods, and beverages. It also finds use in brewing where it alters starches (converting the complex, non-fermentable starches into fermentable sugars) during the malting stage. Further, it is used in the production of baked foods, confectionaries, and other food products as a thickening and moisturizing agent. In pharmaceutical applications, it is used as a diluent and filler in tablet preparations and a source of glucose in intravenous infusion.
The market for Maltose is driven by its usage as a sweetener in valuable food products like candy, bakery products and beverage production, thus raising its market demand in the food, beverage, and baking industries. Its ability to enhance texture and moisture retention in products amplifies its demand in the baking industry. Its employment in convenience foods and ready-to-drink beverages fuels its demand even more. Its use as a natural sweetener makes it marketable than other artificial sweeteners hence increasing its market value. Overall, industrial Maltose procurement is influenced by its usage as a sweetener in the food, beverage, and baking industries, its utilization in ready-to-drink beverages and convenience foods, the availability of its raw materials (starch and glucose), the cost of its raw materials, increasing preference for natural sweeteners, and technological advancements.
Raw Material for Maltose Production
According to the Maltose manufacturing plant project report, the key raw materials used in the production of Maltose include starch; glucose.
Manufacturing Process of Maltose
The extensive Maltose production cost report consists of the following major industrial manufacturing processes:
- Production from hydrolysis of starch: The manufacturing process of Maltose takes place by hydrolysis of starch. Heavy molecules of starch are broken down into smaller ones when reacted with water with the help of enzymes such as amylase to produce Maltose as the final product.
- Production from glucose: The production of Maltose occurs through the condensation process. In this process, two units of glucose are joined together, which leads to the elimination of water molecule to form Maltose as the final product.
Maltose or malt (C12H22O11) is a disaccharide comprising two alpha D glucose units where the two glucose units are linked with an alpha 1,4 glycosidic linkage. It is one of the lower molecular weight carbohydrates, which are a kind of disaccharide sugar. It's a reducing sugar and goes through mutarotation. Maltose is a white crystalline solid with no odour and a sweet sugar-like taste. It has a molar mass of 342.30 g/mol and a density of 1.54 g/cm3. Its melting point is within the range of 160-165 °C. It is soluble in water with a solubility of 1.0 g/mL (at 20 °C). Due to the presence of a high glycemic index, it gives rise to the blood sugar level.
Maltose Production Cost Processes with Cost Analysis
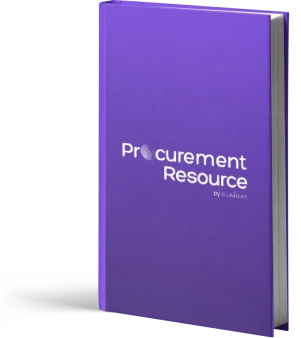
Maltose Production from Hydrolysis
This report provides the cost structure of maltose production from hydrolysis. Heavy molecules of starch are broken down into smaller ones when reacted with water with the help of enzymes.
Details: Germany - based plant Q1 2025 From $ 2499.00 USD
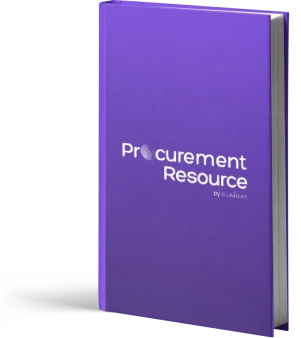
Maltose Production from Condensation Reaction
In this process, two units of glucose are joined together leading to the elimination of water molecule to form a disaccharide, i.e., maltose.
Details: Germany - based plant Q1 2025 From $ 2499.00 USD
Product Details
Particulars | Details |
---|---|
Product Name | Maltose |
Scope | Manufacturing Process: Process Flow, Material Flow, Material Balance Raw Material and Product Specifications: Raw Material Consumption, Product and Co-product Generation Land and Site Cost: Offsites/Civil Works, Equipment Cost, Auxiliary Equipment Costs, Contingency, Engineering and Consulting Charges, Working Capital Variable Cost: Raw Material, Utilities, Other Variable Costs Fixed Cost: Labor Requirements and Wages, Overhead Expenses, Maintenance Charges, Other Fixed Costs Financing Costs: Interest on Working Capital, Interest on Loans Other Costs: Depreciation Charges, General Sales and Admin Cost |
Currency | US$ (Data can also be provided in the local currency) |
Pricing and Purchase Options | Basic: US$ 2499 Premium: US$ 3499 Enterprise: US$ 4799 |
Customization Scope | The report can be customized as per the requirement of the customer |
Post-Sale Analysts Report | 10-12 weeks of post-purchase analyst support after report delivery for any queries from the deliverable |
Delivery Format | PDF and Excel format through email (editable version in PPT/Word format of the report can be also provided on special request) |
How does our Maltose Production Cost Report Provide Exhaustive Data and Extensive Insights?
At Procurement Resource, we not only focus on optimizing the should cost of production for Maltose but also provide our clients with extensive intel and rigorous information on every aspect of the production process. By utilizing a comprehensive cost model, we help you break down expenses related to raw materials, labor, and technology, offering clear pathways to savings. We also assist in evaluating the capital expenditure (CAPEX) and operating expenses (OPEX), which are often measured as cost per unit of production, such as USD/MT, ensuring that your financial planning is aligned with industry benchmarks.
We offer valuable insights on the top technology providers, in-depth supplier database, and best manufacturers, helping you make informed decisions to improve efficiency. Additionally, we design the most feasible layout for your production needs, ensuring the entire process runs smoothly. By minimizing the cash cost of production, we ensure that you stay competitive while securing long-term profitability in the growing Maltose market. Partnering with Procurement Resource guarantees that every aspect of your production is cost-efficient, advanced, and tailored to your specific requirements.
Key Questions Answered in This Report
- What are the key requirements for setting up a Maltose manufacturing plant?
- How is Maltose manufactured?
- What is the process flow involved in producing Maltose?
- What are the raw material requirements and costs for producing Maltose?
- What is the total size of land required for setting up a Maltose manufacturing plant?
- What are the construction requirements for setting up a Maltose manufacturing plant?
- What are the machinery requirements for producing Maltose?
- What are the utility requirements and costs for producing Maltose?
- What are the manpower requirements for producing Maltose?
- What are the average salaries/wages of manpower working in a Maltose manufacturing plant?
- What are the packaging requirements and associated costs for Maltose?
- What are the transportation requirements and associated costs for Maltose?
- What are the capital costs for setting up a Maltose manufacturing plant?
- What are the operating costs for setting up a Maltose manufacturing plant?
- What should be the price of Maltose?
- What will be the income and expenditures for a Maltose manufacturing plant?
Need more help?
- We can tailor the report as per your unique requirements such as desired capacity, future expansion plans, product specifications, mode of financing, plant location, etc.
- We can also provide a flexible, easy-to-use, dynamic excel-based cost-model/ dashboard where you can change the inputs to get different outputs
- Speak to our highly skilled team of analysts for insights on the recent trends and innovations, industry best practices, key success and risk factors, product pricing, margins, return on investment, industry standards and regulations, etc.
- Gain an unparalleled competitive advantage in your domain by understanding how to optimize your business operations and maximize profits
- For further assistance, please connect with our analysts
Compare & Choose the Right Report Version for You

You can easily get a quote for any Procurement Resource report. Just click here and raise a request. We will get back to you within 24 hours. Alternatively, you can also drop us an email at sales@procurementresource.com.
RIGHT PEOPLE
At Procurement Resource our analysts are selected after they are assessed thoroughly on having required qualities so that they can work effectively and productively and are able to execute projects based on the expectations shared by our clients. Our team is hence, technically exceptional, strategic, pragmatic, well experienced and competent.
RIGHT METHODOLOGY
We understand the cruciality of high-quality assessments that are important for our clients to take timely decisions and plan strategically. We have been continuously upgrading our tools and resources over the past years to become useful partners for our clientele. Our research methods are supported by most recent technology, our trusted and verified databases that are modified as per the needs help us serve our clients effectively every time and puts them ahead of their competitors.
RIGHT PRICE
Our team provides a detailed, high quality and deeply researched evaluations in competitive prices, that are unmatchable, and demonstrates our understanding of our client’s resource composition. These reports support our clientele make important procurement and supply chains choices that further helps them to place themselves ahead of their counterparts. We also offer attractive discounts or rebates on our forth coming reports.
RIGHT SUPPORT
Our vision is to enable our clients with superior quality market assessment and actionable evaluations to assist them with taking timely and right decisions. We are always ready to deliver our clients with maximum results by delivering them with customised suggestions to meet their exact needs within the specified timeline and help them understand the market dynamics in a better way.
SELECT YOUR LICENCE TYPE
- Review the available license options and choose the one that best fits your needs. Different licenses offer varying levels of access and usage rights, so make sure to pick the one that aligns with your requirements.
- If you're unsure which license is right for you, feel free to contact us for assistance.
CLICK 'BUY NOW'
- Once you've selected your desired report and license, click the ‘Buy Now’ button. This will add the report to your cart. You will be directed to the registration page where you’ll provide the necessary information to complete the purchase.
- You’ll have the chance to review your order and make adjustments, including updating your license or quantity, before proceeding to the next step.
COMPLETE REGISTRATION
- Enter your details for registration. This will include your name, email address, and any other necessary information. Creating an account allows you to easily manage your orders and gain access to future purchases or reports.
- If you already have an account with us, simply log in to streamline the process.
CHOOSE YOUR PAYMENT METHOD
- Select from a variety of secure payment options, including credit/debit cards, PayPal, or other available gateways. We ensure that all transactions are encrypted and processed securely.
- After selecting your payment method, you will be redirected to a secure checkout page to complete your transaction.
CONFIRM YOUR PURCHASE
- Once your payment is processed, you will receive an order confirmation email from sales@procurementresource.com confirming the dedicated project manger and delivery timelines.
ACCESS YOUR REPORT
- The report will be delivered to you by the project manager within the specified timeline.
- If you encounter any issues accessing your report, project manager would remain connected throughout the length of the project. The team shall assist you with post purchase analyst support for any queries or concerns from the deliverable (within the remit of the agreed scope of work).