The Healthcare Industry Benefits from On-Demand, Custom Manufacturing
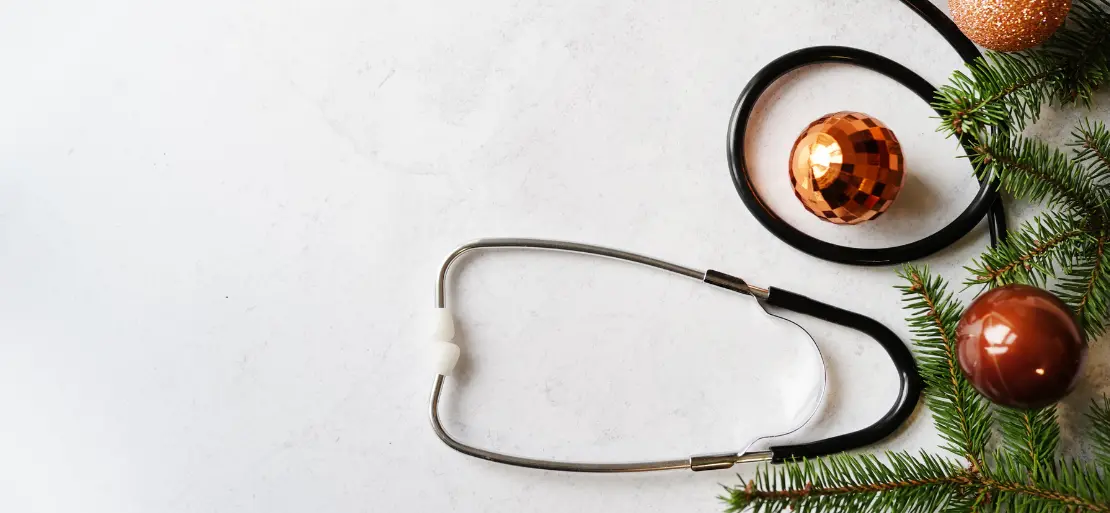
As a leader in custom manufacturing, Xometry is an excellent choice for many manufacturing projects ranging from cutting-edge prototyping to mass production. Customers in the medical field benefit from the capability to customise designs and products, short lead times, high precision parts, and scalability and repeatability for large production volumes. CNC machining is a technology that produces exceptionally accurate metal parts and can handle complex shapes and contours. CNC machining is ideal for manufacturing surgical instruments and tools.
3D printing is primarily used to create products out of plastics, resins, and elastomers, but metal 3D printing is also possible. Carbon DLS enables the fabrication of engineering elastomers with rubber-like strength and resilience. This technology has a variety of applications in the medical field. Injection moulding is a technique while plastic injection moulding is a low-cost method of producing high-precision, accurate, and high-quality parts for the medical industry.
Another reason Xometry is the ideal partner for sourcing parts is its access to a wide range of biocompatible materials. These materials, frequently used in joints, bone plates, and material devices, should be engineered to interact with biologically active systems.
Cobalt chromium and titanium (Ti6AL4V) are biocompatible metals that can be used for implants due to their high tensile strength and corrosion resistance. In contrast, stainless steel and aluminium are used mainly for equipment and tools.
Biocompatible plastics are plastics that offer more options for complexity and customisation. ABS, Nylon PA 12, ULTEM 1010, CE 221, Silicone (Sil 30), and True Silicone all have different properties (heat resistance, corrosion resistance, and flexibility) that can meet the needs of specific parts and designs.
The gradual development of new additive manufacturing technologies and the precision of processes such as injection moulding and CNC machining has resulted in more applications in the medical and healthcare industries. Personal Medical Devices (PMDs) account for a sizable portion of the medical industry's custom manufacturing applications.
3D printing enables the high customization required for these devices (implants, orthotics, prosthetics, bionics). CNC milling's speed and scalability make it ideal for mass production, general-purpose equipment, and surgical devices. It's also a good option for making replacement parts for medical equipment. CNC machining is suitable for small details and body implants due to its tight tolerances (±0.05 mm, ±0.025 with micromachining).
International standards like ISO 13485, ISO 10993, and ISO 9001:2015 strictly govern manufacturing technologies like CNC machining, 3D printing, injection moulding, and biocompatible materials. These certifications, as well as certificates for various materials, are available from Xometry.
Xometry has gained extensive experience in manufacturing parts for the healthcare and medical industries. The company has backed innovative projects such as Viralink, a device that destroys viruses in the air. In a short period, Xometry provided CNC machined parts to Paul Byrne, a British engineer.
Using Xometry, he was able to source a variety of parts for his Viralink devices in less than five weeks. Furthermore, ClearMask, a medical supplies company, benefited from Xometry's supply chain solutions. The company was able to cope with shortages during the pandemic by scaling up production and producing millions of masks in just a few months.